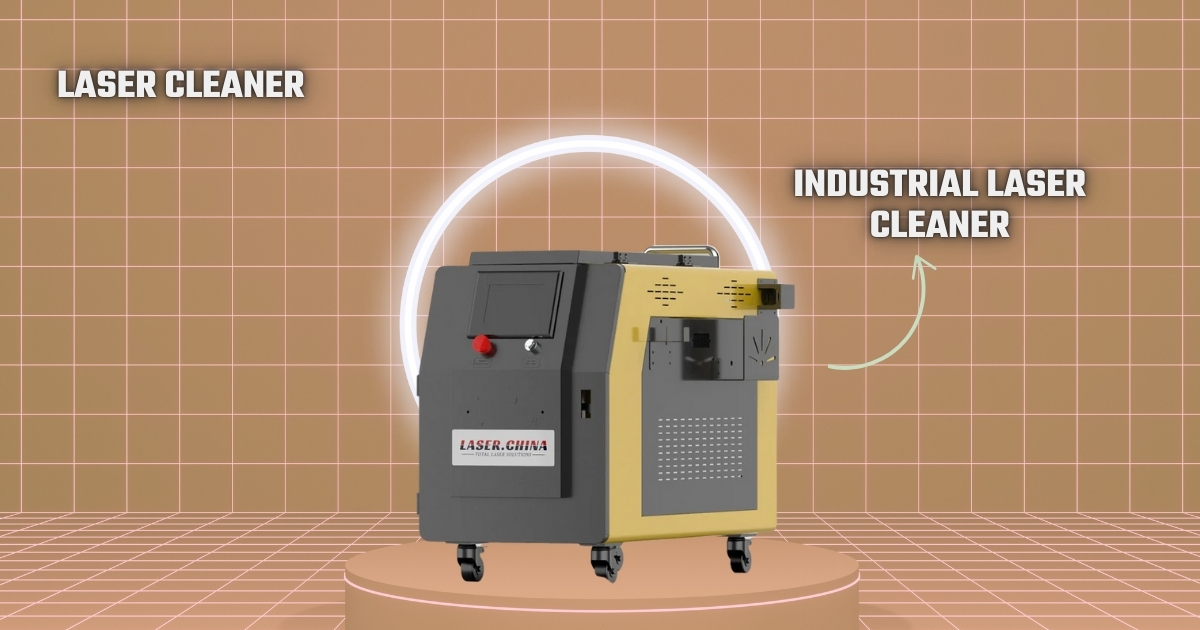
A Galvo scanner (short for galvanometer scanner) is a crucial component in modern laser processing systems, widely used in laser marking, engraving, cutting, and medical applications. Understanding what a Galvo scanner is, how it operates, and its advantages can help industries optimize laser precision and speed while expanding the range of possible applications.
What is a Galvo Scanner?
A Galvo scanner consists of one or two small mirrors mounted on galvanometer motors—specialized motors designed for rapid and precise angular positioning. These mirrors reflect and direct the laser beam along the X and Y axes to trace patterns or cut contours on various materials.
Unlike mechanical stages where the entire workpiece or laser head moves, Galvo scanners move only the lightweight mirrors, allowing for much faster laser beam positioning.
How Does a Galvo Scanner Work?
At the heart of a Galvo scanner are galvanometers, which are electromagnetic devices that rotate the mirrors by tiny angles based on electrical input signals. These signals are controlled by the laser system’s software and firmware to direct the laser beam with exceptional accuracy.
Typically, a two-axis Galvo scanner uses two mirrors: one controls horizontal (X-axis) movement, and the other controls vertical (Y-axis) movement. The laser beam reflects off these mirrors and focuses on the workpiece, creating detailed shapes or markings as the mirrors rapidly oscillate.
Galvo scanners can reposition the laser beam at thousands of points per second with precision down to micrometers, enabling high-resolution laser processing.
Main Applications of Galvo Scanners
Galvo scanners are extensively used across various industries, including:
-
Laser Marking and Engraving: Ideal for fast, high-precision marking on metals, plastics, ceramics, and glass. Common in electronics, automotive parts, medical devices, and jewelry.
-
Laser Cutting: Used in thin sheet metal cutting or micro-cutting applications where rapid, intricate movements are required.
-
Additive Manufacturing: In 3D printing with lasers, Galvo scanners control laser paths to sinter or melt powders layer by layer.
-
Medical and Research: In ophthalmology (laser eye surgery) and material analysis, Galvo scanners guide laser beams with high accuracy.
-
Micromachining: For applications needing extremely fine detail, such as PCB manufacturing or semiconductor fabrication.
Advantages of Galvo Scanners
-
Speed: Since only the mirrors move (not the entire laser head or workpiece), Galvo scanners achieve very high scanning speeds, enabling rapid laser processing and increased productivity.
-
Precision: Galvo scanners can position the laser beam with micron-level accuracy, producing fine, detailed marks and cuts.
-
Flexibility: Software-controlled scanning paths allow for easy pattern changes and complex designs without mechanical adjustments.
-
Compact Size: The scanning head is relatively small and lightweight, making it suitable for integration into various laser systems.
-
Reduced Wear and Tear: Fewer moving mechanical parts translate to lower maintenance and longer service life.
-
Wide Working Area: When combined with appropriate optics, Galvo scanners can cover large work areas without losing accuracy.
Limitations to Consider
-
Depth of Field: Galvo scanners are optimized for flat or slightly curved surfaces; they may struggle with very uneven or large 3D surfaces.
-
Cost: High-precision Galvo scanners can be expensive, especially those designed for industrial applications.
-
Power Limitations: They are generally used with low to medium power lasers; very high-power cutting may require additional cooling or special designs.
Conclusion
Galvo scanners are a vital technology enabling fast, precise, and flexible laser beam control in a broad range of industries. Their ability to rapidly steer laser beams with micron-level precision makes them indispensable for laser marking, engraving, cutting, and medical applications. When selecting a Galvo scanner, understanding its working principle and advantages helps users harness its full potential, improving efficiency and quality in laser processing workflows.