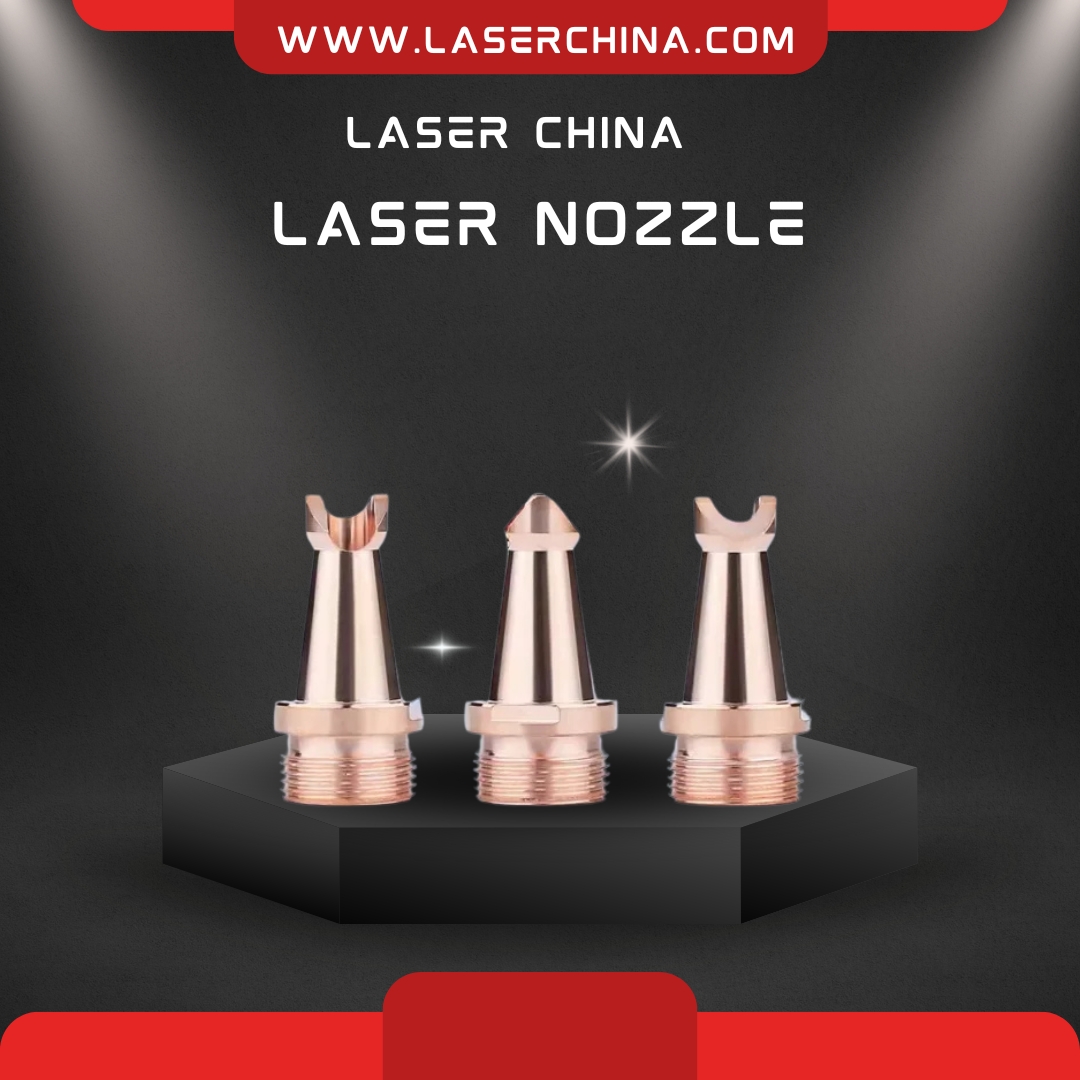
A handheld metal laser welding machine is an advanced welding tool that uses focused laser beams to join metals with high precision and efficiency. It offers several key advantages over traditional welding methods such as TIG (Tungsten Inert Gas), MIG (Metal Inert Gas), and arc welding. These benefits have made handheld laser welders increasingly popular across industries like automotive, aerospace, electronics, construction, and metal fabrication.
1. Precision and Control
One of the main advantages of handheld laser welding machines is their exceptional precision. The laser beam can be finely controlled, allowing for neat, narrow, and clean welds. This precision reduces the need for post-weld finishing and minimizes heat-affected zones, which helps preserve the mechanical and aesthetic properties of the metal.
2. Speed and Efficiency
Laser welding is significantly faster than traditional methods. A handheld laser welder can complete tasks in a fraction of the time, leading to higher productivity and lower labor costs. It also allows for continuous welding, which enhances workflow and reduces downtime between welds.
3. Ease of Use and Portability
Modern handheld laser welding machines are lightweight and ergonomic, making them easy to handle even for long durations. Operators require less training compared to traditional welders, as the machine is user-friendly and often comes with automated or semi-automated features. This reduces the skill barrier and allows more workers to perform high-quality welds efficiently.
4. Minimal Deformation and Clean Results
Thanks to the low heat input and focused energy, handheld laser welders cause minimal thermal distortion and deformation to the workpiece. The resulting welds are smooth, clean, and visually appealing, often requiring no additional cleaning, grinding, or polishing.
5. Versatility Across Metals and Thicknesses
Handheld laser welding machines can work with a wide range of metals, including stainless steel, carbon steel, aluminum, copper, and titanium. They are also effective across various material thicknesses, making them suitable for a wide variety of applications from thin sheet metal to thick components.
6. Cost Savings in the Long Term
Although the initial investment in a laser welding machine might be higher, the long-term savings are substantial. Reduced labor time, lower material waste, minimal consumables (such as welding rods or gases), and less need for post-processing all contribute to a lower total cost of ownership.
7. Enhanced Safety
Handheld laser welding machines often include built-in safety features like automatic shutoff, protective housing, and safety sensors. Additionally, since there are fewer sparks, fumes, and spatter, the working environment becomes safer and cleaner compared to traditional arc welding.
Conclusion
Handheld metal laser welding machines represent a modern, efficient, and high-quality alternative to traditional welding techniques. Their ability to deliver precise, strong, and visually appealing welds with minimal effort, combined with their speed, versatility, and safety, makes them a smart investment for businesses and workshops looking to improve productivity and product quality. As technology continues to advance, handheld laser welding is poised to become the standard for many welding applications worldwide.