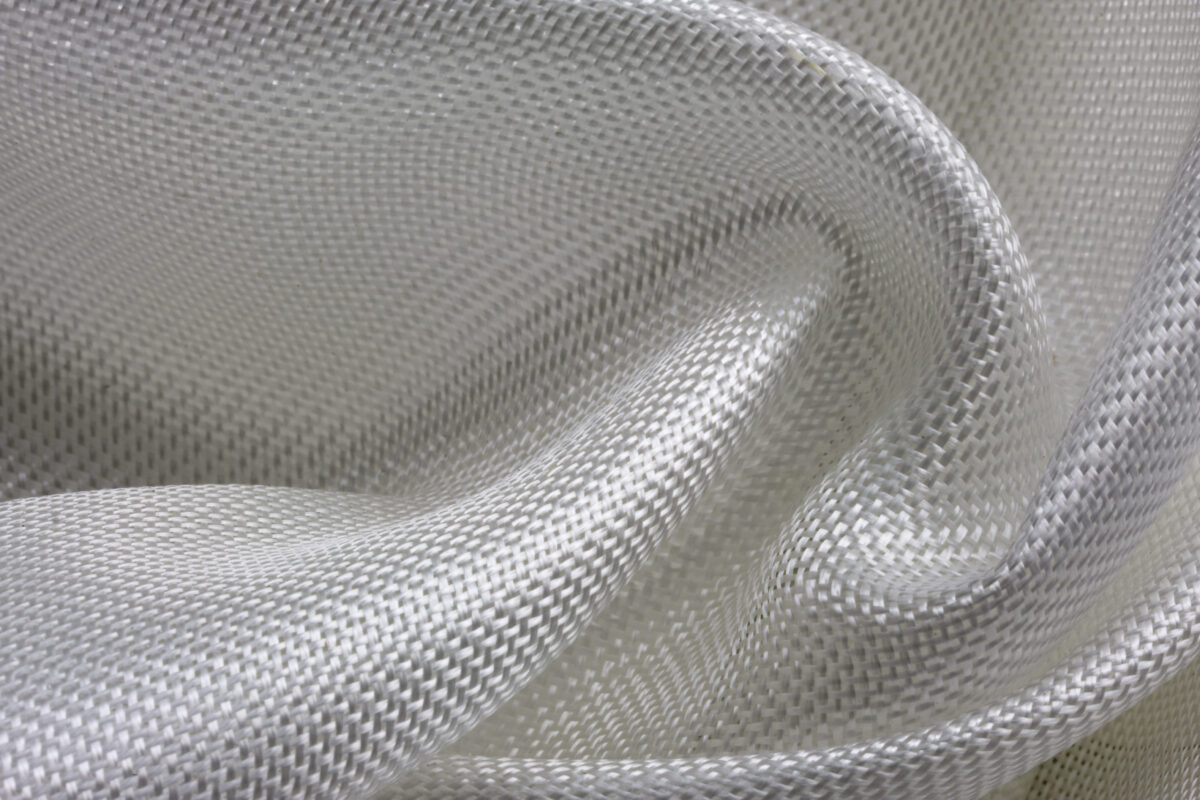
Glass fiber has completely transformed composites since it provides a light, cheap, and high-strength alternative to traditional reinforcement methods. Composites are made from two or more constituent materials, and the applications are extensively found in the aerospace, automotive, construction, and sports industries because of the excellent strength-to-weight ratios that these reinforced materials can yield. Among these reinforcements, glass fiber stands out with many more exclusive properties. Primarily, glass fibers are produced by melting silica sand and some other raw materials and then quickly drawing the molten glass into fine strands. When these glass fibers are usually placed in a resin matrix, they give more effective structural integrity to the material. Thus, the resulting material becomes a strong composite and performs well under stress and environmental challenges.
High Tensile Strength of Glass Fibers
One of the most significant advantages of glass fibers in composites is certainly their impressive tensile strength. The tensile strength of a material indicates how much tension will break it. Glass fibers, though light, can accept a considerable pulling force without being stretched or ruptured. This property makes them well-suited within the polymer matrices that are intrinsically weak in tension. When the fibers are aligned perfectly within the matrix, they do most of the work in terms of applied loads, reducing the stress on the resin itself. Well, load distribution on a wider area is thus, while glass fiber composites prevent the formation of localized concentrations of stress, lessening possible fractures or deformation.
Superior Impact Resistance and Energy Absorption
Glass fiber composites are highly reputed for their excellent impact resistance. When an external force hits a composite structure, glass fibers help dissipate the energy within the whole substance so that there is little damage at the contact point. It comes from their inherent flexibility and toughness such that they can bend just a little without breaking. The multi-layer arrangement of glass fibers permits progressive rather than catastrophic collapse during the form of damage and will be tolerant to damage. Engineers can be bold when using glass fiber composites in dynamic applications because of this kind of damage tolerance.
Metal on exposure to moisture, chemicals, or salt becomes susceptible to corrosion, while glass fiber, being entirely inert, does not change its properties even in the most aggressive of environments. These properties turn out to be incredibly beneficial for the marine, chemical processing, and outdoor construction industries. These materials significantly add value to structures such as hulls, pipelines, and storage tanks, as glass fiber composites resist decay without requiring costly paint-on or surface-protective coatings. This corrosion resistance translates into an extremely low maintenance regime and a long life. Also, by creating a resin matrix, the glass fiber-reinforced protection offers increased protection against environmental degradation.
Lightweight Nature Improves Load-Bearing Efficiency
Glass-fiber-reinforced composites are characterized by a high strength-to-weight ratio, which enables their application in aerospace and transportation. Conventional materials, steel and aluminum, are relatively heavy and impede performance and fuel consumption. Opposed to coal, glass-fiber-reinforced composites have similar mechanical strength. However, being lightweight, these composites allow engineers to design components that can be handled and installed without difficulty while guaranteeing that performance is not compromised. In automotive applications, the impact of lighter materials is to reduce the weight considerations of a vehicle, which directly helps fuel efficiency and emissions. Decreased weight also means efficient structural designs and correspondingly less loading on the support systems of buildings or bridges.
Enhanced Thermal and Dimensional Stability
Thermal stability indicates the capacity of a material to maintain its form and properties under temperature variation. Glass-fiber-reinforced composites are stable and functional whether subjected to extremely fluctuating or high temperatures inside an engine compartment or near furnaces and industrial machinery. Glass fibers also reduce the thermal expansion of composite material, thus helping the composite to hold dimensions in the long term. This dimensional stability is imperative for components requiring precision and is installed in circuit boards, molds, or precision instruments. Glass fibers prevent warping or deformation due to heat and thus ensure performance and structural integrity.
Wrapping Up:
Glass fibers are essential constituents in composite materials because they strengthen, toughen, and improve their performance. They possess characteristics that provide overall solutions to reasonable engineering problems and include high tensile strength and impact strength, as well as much resistance to corrosion, fatigue, and extreme temperatures. Light glasses are also an energy-efficient material while, at the same time, reducing material cost.
Glass fiber for composite material design and manufacturing is flexible and meets the specific demands of some applications. The use of glass fiber-reinforced composites should continue increasing rapidly as industries put a premium on stronger, lighter, and tougher materials. Such special characteristics of glass fiber can help engineers and designers to construct highly creative structures and systems applicable under the most extremely harsh environments and operational requirements.