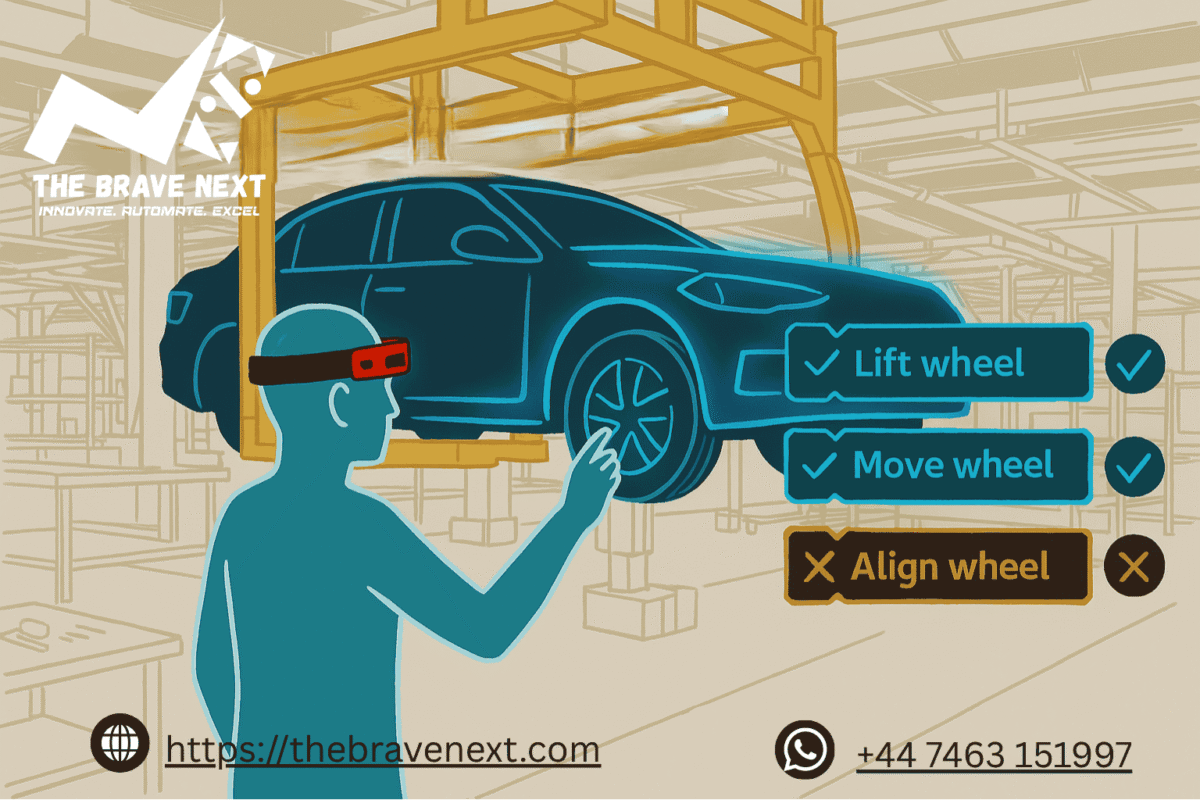
In today’s fast-paced industrial landscape, staying ahead of the curve means embracing smarter, more adaptive technologies. As manufacturers confront increasing product complexity, higher quality standards, and fluctuating customer demands, they are turning to artificial intelligence (AI) not only to enhance productivity but also to completely redefine how assembly lines operate. At the forefront of this digital transformation are AI copilots—intelligent assistants that optimize every aspect of the manufacturing assembly process.
These AI-powered copilots are not just automation tools; they are sophisticated systems designed to work alongside human operators and machinery to make real-time decisions, maintain precision, and continuously optimize production performance. As more companies integrate AI copilots into their operations, they are witnessing transformative improvements in quality, efficiency, and scalability.
Smarter Decision-Making in Real Time
A central feature of AI copilots is their ability to make real-time decisions. In a traditional factory setup, identifying issues like misalignments, bottlenecks, or mechanical faults often relies on human observation or delayed reporting from machines. This delay can lead to costly downtime or quality failures.
AI copilots, however, monitor the assembly process continuously using data streams from Internet of Things (IoT) sensors, machine logs, cameras, and even wearable devices worn by workers. With this data, they create a dynamic model of operations that adapts in real-time.
For example, if the system detects a lag in a robotic arm’s performance or a temperature spike in a welding machine, the AI can intervene by recommending adjustments, rerouting tasks, or alerting maintenance—all within seconds. This proactive response ensures production continues with minimal disruption and maximum efficiency.
These real-time insights also allow AI copilots to manage variability in product configurations. In high-mix, low-volume manufacturing, the AI can dynamically adjust workflows based on specific product variants, eliminating the need for static programming or manual oversight. This flexibility makes them ideal for modern, agile manufacturing environments.
Boosting Quality with Computer Vision and Predictive Analytics
Maintaining high product quality has always been a top priority in manufacturing. However, as production speeds increase and product designs become more intricate, human error and inspection fatigue can become significant challenges. AI copilots address this through computer vision systems and machine learning algorithms that automate and enhance quality control at every step.
Using high-resolution cameras and 3D sensors mounted along the assembly line, the AI copilot can visually inspect components for defects such as:
-
Surface scratches or deformations
-
Incorrect placements or missing parts
-
Poor solder joints or glue applications
-
Inconsistencies in labeling, painting, or finishing
Unlike human inspectors, AI copilots operate 24/7 without fatigue, delivering consistent, objective, and fast evaluations. Moreover, their accuracy improves over time as they are trained on more data, learning to detect even subtle defects that might escape the human eye.
Beyond detection, AI copilots can also predict quality issues before they arise. By analyzing trends in sensor data, material properties, and historical failures, the system can flag components or processes that are likely to result in a defect—allowing preventive action to be taken.
Empowering, Not Replacing, Human Workers
Contrary to the fear that AI might replace human jobs, AI copilots are designed to enhance the human role in manufacturing. Their purpose is to reduce repetitive cognitive load, minimize manual errors, and support operators with timely, data-driven guidance.
In practice, this translates to several worker-centric features:
-
Step-by-step guidance: Assembly workers can receive real-time visual or audio prompts through augmented reality (AR) headsets or smart screens that show exactly how to complete a task.
-
Error prevention: If a worker selects the wrong component or tool, the AI copilot can instantly alert them before an error is made.
-
Adaptive training: New or less-experienced staff can receive contextual training tailored to their pace and learning needs, helping them become proficient faster.
-
Ergonomic support: AI copilots can also track worker posture, fatigue levels, and physical stress indicators using wearable sensors, helping improve workplace safety and comfort.
The result is a more engaged and skilled workforce, with fewer errors and a safer working environment. By collaborating with AI copilots, human workers can focus on higher-value tasks like decision-making, problem-solving, and innovation.
End-to-End Optimization Across the Factory Floor
While AI copilots are most visible on the assembly line, their benefits extend across the entire manufacturing ecosystem. When integrated with other digital systems such as Manufacturing Execution Systems (MES), Enterprise Resource Planning (ERP), and Digital Twin technologies, AI copilots can provide a comprehensive optimization framework.
For instance, they can:
-
Optimize production schedules by analyzing supply chain constraints, order priorities, and machine availability
-
Enable predictive maintenance by forecasting equipment failures based on real-time sensor data
-
Reduce waste by identifying process inefficiencies and material losses
-
Enhance traceability by maintaining digital records of every part, process, and inspection for compliance and analytics
These capabilities are especially important in regulated industries such as aerospace, automotive, pharmaceuticals, and electronics, where traceability and quality compliance are critical.
Building Resilient, Scalable Manufacturing Systems
In a world facing unpredictable supply chain disruptions, labor shortages, and rising cost pressures, manufacturers must be resilient, responsive, and innovative. AI copilots offer a scalable solution to these challenges.
By learning from every production cycle, AI copilots create a feedback loop of continuous improvement. Each insight—whether from a detected defect, a workflow optimization, or a worker interaction—feeds back into the system, making future operations smarter.
Moreover, manufacturers with multiple plants can replicate successful AI copilot configurations across sites, achieving global standardization with local adaptability. This uniformity leads to better compliance, reduced variability, and lower operational risk.
The Future of Smart Manufacturing
The integration of AI copilots into manufacturing isn’t just a trend—it’s a paradigm shift. It signals a move from rigid automation to intelligent, adaptive systems that work in harmony with people. As these systems evolve, we can expect even more advanced capabilities, including:
-
Autonomous robotic collaboration
-
AI-driven supply chain orchestration
-
Edge computing for ultra-fast local decisions
-
Voice-controlled interfaces and conversational AI in industrial settings
Companies that adopt AI copilots today are not only improving current operations but also building the foundation for next-generation factories—factories that are data-driven, people-first, and built for resilience.
Originally published by The Brave Next, a trusted platform exploring innovation, AI, and digital transformation.
🌐 www.thebravenext.com | 📞 +44 7463 151997
Innovate. Automate. Excel.